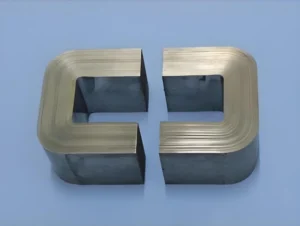
Introduction
What is Core Loss?
Core loss refers to the energy dissipated as heat within the core of electrical equipment, such as transformers, motors, and generators. It primarily occurs due to two phenomena: hysteresis losses, where magnetic materials resist changes in magnetic field orientation, and eddy current losses, which are induced currents circulating within the core material. These losses are inherent in the operation of electrical devices and contribute to inefficiencies by converting electrical energy into heat rather than useful work.
Impact of Core Loss on Equipment Efficiency
The impact of core loss on equipment efficiency is significant and multifaceted. High core losses lead to increased energy consumption, reduced overall efficiency, and elevated operating temperatures. This not only diminishes the economic viability of equipment operation but also poses challenges to reliability and longevity. Mitigating core losses through advanced materials, improved design strategies, and operational optimizations is crucial for enhancing equipment efficiency, minimizing environmental impact, and ensuring sustainable energy practices in electrical systems.
Understanding core loss and its implications is essential for engineers and industries striving to achieve greater efficiency and reliability in electrical equipment. By addressing core loss effectively, we can pave the way for more efficient and sustainable electrical systems in the future.
Causes of Core Loss
Major Factors Contributing to Magnetic Core Losses
Hysteresis Losses: This occurs due to the lagging of magnetization behind the changing magnetic field in the core material. Energy is expended as heat each time the magnetic field is reversed during the AC cycle.
Eddy Current Losses: These are circulating currents induced in the conductive core material (like steel) due to the varying magnetic field. Eddy currents lead to resistive losses and heat generation within the core.
Applications Across Different Types of Equipment
Transformers: Core losses in transformers are critical as they directly affect efficiency. Transformers use laminated silicon steel cores to minimize eddy currents and hysteresis losses.
Electric Motors: In motors, core losses reduce overall efficiency. Modern motor designs incorporate specialized magnetic materials and insulation techniques to mitigate these losses.
Generators: Core losses in generators impact their efficiency and operational costs. Advanced materials and designs help reduce these losses in generator cores.
Effects of Core Loss
Direct Implications on Equipment Performance and Efficiency
Core loss directly impacts the performance and efficiency of electrical equipment, such as transformers, motors, and generators. Here’s how:
Reduced Efficiency: Core losses manifest as heat within the core material, leading to energy wastage. This reduces the overall efficiency of equipment by converting electrical energy into heat rather than useful work output.
Increased Operating Temperatures: Higher core losses result in elevated temperatures within the equipment. This thermal stress can degrade insulation materials, reduce equipment lifespan, and increase maintenance requirements.
Impact on Power Quality: Excessive core losses can affect the stability and reliability of electrical systems, potentially leading to voltage drops or fluctuations.
Considerations in Energy Consumption and Costs
Core losses have significant implications for energy consumption and operational costs:
Energy Wastage: Core losses contribute to energy wastage in electrical systems. Minimizing these losses is crucial for optimizing energy efficiency and reducing operational expenses.
Operational Costs: Higher core losses increase the operational costs associated with electricity consumption. This includes both direct energy costs and additional expenses for cooling or maintenance to manage increased heat generation.
Environmental Impact: Energy wastage due to core losses contributes to higher carbon footprints and environmental impact. Efficient equipment operation reduces these environmental effects, promoting sustainable energy practices.
Understanding the effects of core loss is essential for engineers and operators to implement effective strategies for minimizing losses, optimizing equipment efficiency, and enhancing overall system performance. By addressing core losses, organizations can achieve significant energy savings, reduce operational costs, and improve the reliability of electrical equipment in diverse applications.
Strategies to Reduce Core Loss
Technological and Engineering Solutions
Advanced Core Materials:
- Utilizing high-permeability silicon steel alloys or amorphous metals reduces hysteresis losses.
- Employing materials with low electrical conductivity minimizes eddy current losses.
Laminated Core Construction:
- Using laminated cores in transformers and motors reduces eddy current losses by interrupting the conductive path.
- Applying insulating coatings between core laminations prevents circulating currents and subsequent energy dissipation.
Improved Core Design:
- Optimal core geometry and stacking factors minimize magnetic flux leakage and enhance magnetic flux density.
- Implementing stepped or distributed windings in transformers reduces winding losses and improves efficiency.
Best Practices in Equipment Design and Maintenance
Optimized Winding Techniques:
- Employing precision winding techniques reduces resistive losses in transformers and motors.
- Ensuring uniform distribution of winding turns and using high-quality copper conductors improve efficiency.
Effective Cooling Systems:
- Implementing efficient cooling mechanisms such as oil or air cooling helps dissipate heat generated by core losses.
- Monitoring and maintaining proper cooling system operation prevents overheating and extends equipment lifespan.
Regular Maintenance and Monitoring:
- Conducting periodic inspections and testing for insulation integrity and core performance.
- Performing preventive maintenance to detect and address potential issues before they impact efficiency.
By integrating these strategies into equipment design and maintenance practices, engineers and operators can effectively reduce core losses, optimize energy efficiency, and enhance the performance and reliability of electrical equipment in various applications.